Exotic Steel
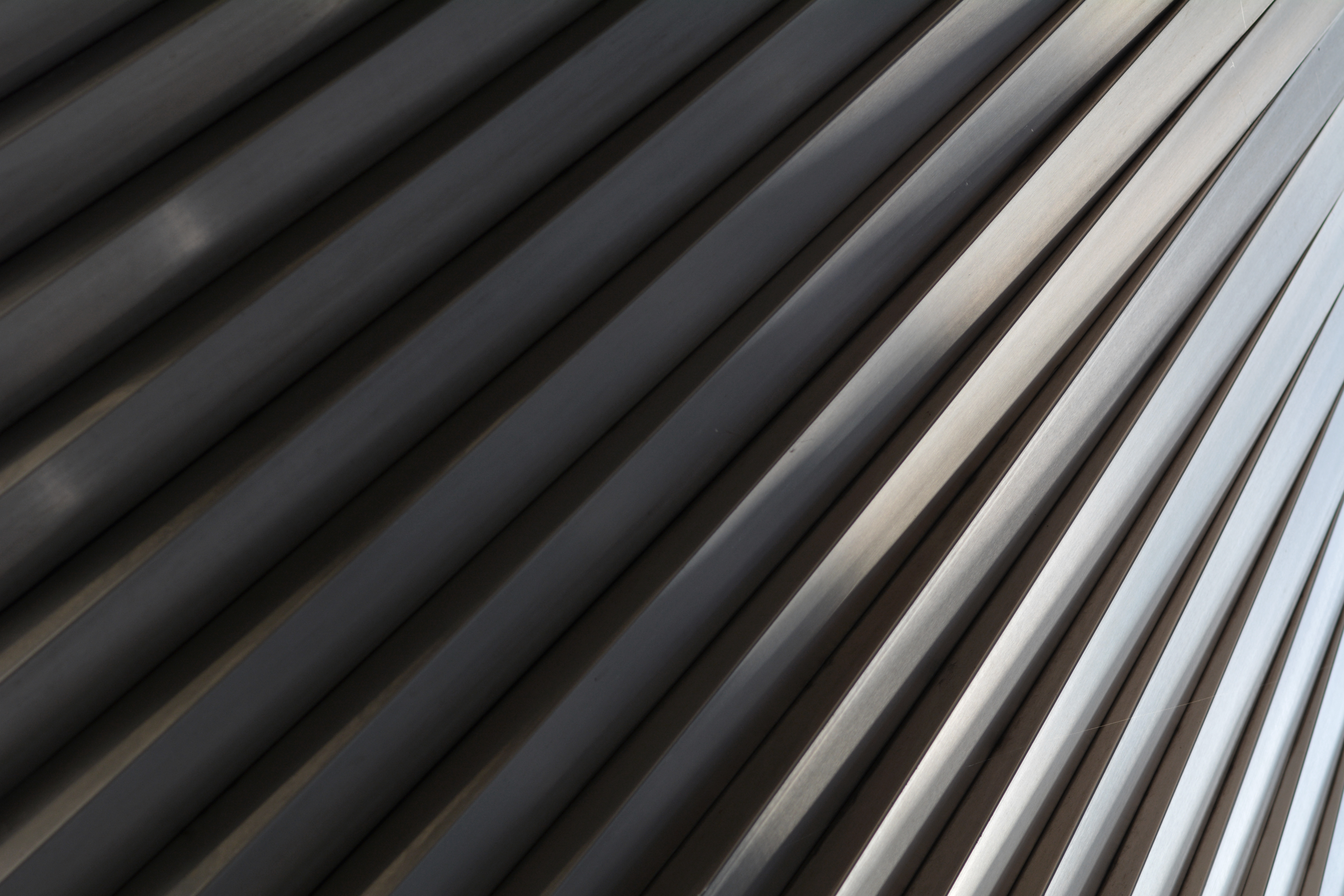
Super alloys, also known as high-performance alloys or exotic alloys, are a class of metallic materials engineered to exhibit exceptional mechanical strength, corrosion resistance, creep resistance, and thermal stability at elevated temperatures. These alloys are extensively used in industries where extreme conditions and demanding applications are encountered. Here are some key aspects of super alloys:
-
Composition:
- Super alloys are typically composed of a base metal (often nickel, cobalt, or iron) with significant additions of alloying elements such as chromium, molybdenum, tungsten, titanium, and sometimes aluminum or niobium.
- The combination of base metals and alloying elements imparts unique properties to super alloys, including high temperature strength, oxidation resistance, and thermal stability.
-
Properties:
- High Temperature Strength: Super alloys exhibit exceptional strength and mechanical properties at elevated temperatures, making them suitable for use in high-temperature environments such as gas turbines, jet engines, and rocket propulsion systems.
- Oxidation and Corrosion Resistance: Super alloys are highly resistant to oxidation, corrosion, and degradation in aggressive environments, including those containing acids, alkalis, and high-temperature gases.
- Creep Resistance: Super alloys possess excellent creep resistance, allowing them to maintain structural integrity and dimensional stability under prolonged exposure to high temperatures and mechanical stress.
- Thermal Stability: Super alloys maintain their mechanical properties and microstructure over a wide range of temperatures, providing stability and reliability in thermal cycling and fluctuating operating conditions.
-
Types of Super Alloys:
- Nickel-Based Alloys: Nickel-based super alloys are the most widely used type and find applications in aerospace, power generation, chemical processing, and marine industries. They offer excellent strength, corrosion resistance, and thermal stability.
- Cobalt-Based Alloys: Cobalt-based super alloys are known for their exceptional high-temperature strength and resistance to thermal fatigue. They are commonly used in gas turbine engines, nuclear reactors, and medical implants.
- Iron-Based Alloys: Iron-based super alloys, also known as super ferritic alloys, offer a combination of high strength, corrosion resistance, and magnetic properties. They are used in applications such as automotive exhaust systems, heat exchangers, and marine components.
- Titanium-Based Alloys: Titanium-based super alloys combine the lightweight properties of titanium with the high-temperature strength and corrosion resistance of other alloying elements. They are used in aerospace, chemical processing, and biomedical applications.
-
Applications:
- Aerospace and Aviation: Super alloys are extensively used in aircraft engines, gas turbines, and aerospace components subjected to high temperatures and mechanical stress.
- Power Generation: Super alloys are employed in gas and steam turbines, nuclear reactors, and power plant components requiring high temperature and corrosion resistance.
- Chemical Processing: Super alloys find application in chemical reactors, heat exchangers, and process piping systems handling corrosive chemicals and high temperatures.
- Oil and Gas: Super alloys are used in oil and gas exploration and production equipment, including downhole tools, valves, and tubing, where high temperature and corrosion resistance are critical.
- Medical: Super alloys are utilized in medical implants such as orthopedic implants, dental prosthetics, and surgical instruments due to their biocompatibility, corrosion resistance, and mechanical strength.
-
Manufacturing and Processing:
- Super alloys are typically produced through advanced metallurgical processes such as vacuum melting, powder metallurgy, and directional solidification to ensure uniform composition, microstructure, and mechanical properties.
- Precision machining, forging, and heat treatment techniques are employed to fabricate super alloy components with complex geometries and stringent dimensional tolerances.
-
Challenges:
- Super alloys often pose challenges in machining and fabrication due to their high hardness, toughness, and work hardening tendencies.
- The high cost of raw materials and manufacturing processes associated with super alloys can make them economically prohibitive for certain applications.
Super alloys represent a pinnacle of material science and engineering, offering unparalleled performance in extreme environments where conventional materials would fail. Their unique combination of properties makes them indispensable in critical industries such as aerospace, power generation, and chemical processing, driving innovation and technological advancement.
Lincoln Structural has the knowledge and expertise to not only supply but manufacture products made from these exotic materials. Contact us today for any of your exotic material needs.